Cleanrooms are indispensable to the labs and professions that use them. Certain fields, like life sciences, electronics, food manufacturing and pharmaceuticals must refine their products and conduct research in a sanitary environment with zero pollution. Therefore, airborne contaminants of any kind cannot enter the work space. Cleanrooms present the solution.
Often, cleanrooms are known as “controlled environments.” Ultimately, their purpose is to inhibit airborne particles and other environmental matter. Most use a laminar airflow system, entryway air showers and strict employee protocol to ensure maximum cleanliness and minimal pollution. Additionally, the structure of the cleanroom itself is usually engineered and constructed in a way that also limits the introduction of particles. Of course, each lab must routinely ensure their cleanroom is maintaining industry standards and functioning properly. Testing and certification services verify that the cleanroom meets the proper industry requirements. In this post, we’ll explore the basics of cleanroom testing and certification and explore what you should expect from each.
Cleanroom Testing
First and foremost, cleanroom testing is about verifying that all features operate as they should. Rooms are classified by the number of particles per cubic meter per minute. Classifications are described in ISO-14644-1, and they range from ISO class 1 through 9. Based on these classifications, technicians know precisely how they should quantify and evaluate performance.
Of course, every cleanroom combines several different features in order to inhibit pollutants. HEPA filtration, laminar air flow and entryway air showers are just a few cleanroom staples. Usually, every cleanroom has all three of these features. Of course, the more advanced cleanrooms which demand higher efficiency, often have many more features and stricter policies. In order to test how the cleanroom is working, technicians perform a few specific tests. Ultimately, cleanroom tests determine efficiency once they measure the number of particles in the air.
Airflow Volume/Velocity Test
The air velocity test confirms that both airflow patterns (unidirectional and non-unidirectional) have a proper balance. Technicians test the air flow velocity using a duct or a vent. They calculate the air exchange rate, and document all air flow velocity parameters with precise measuring instruments.
Additionally, the airflow volume test measures the air volume flow with a volume flow hood. The hood captures and contains the air coming from each filter or diffuser in the room. As a result, the technician can discern that the air patterns are compelling air throughout and out of the room as necessary.
HEPA Filter Integrity Test
HEPA filters can remove 100% of airborne particles above 5µm. Below that, they’re less effective. Usually, they will remove 95% to 99.9995% in the 0.15µm to 0.25µm particle size range. Ultimately, the filter’s grade determines the general filtration efficiency.
Technicians test the HEPA filters within the cleanroom to ensure they’re leak free. With zero signs of leaks or abrasions in the filter, the technician can confirm it’s working as it should.
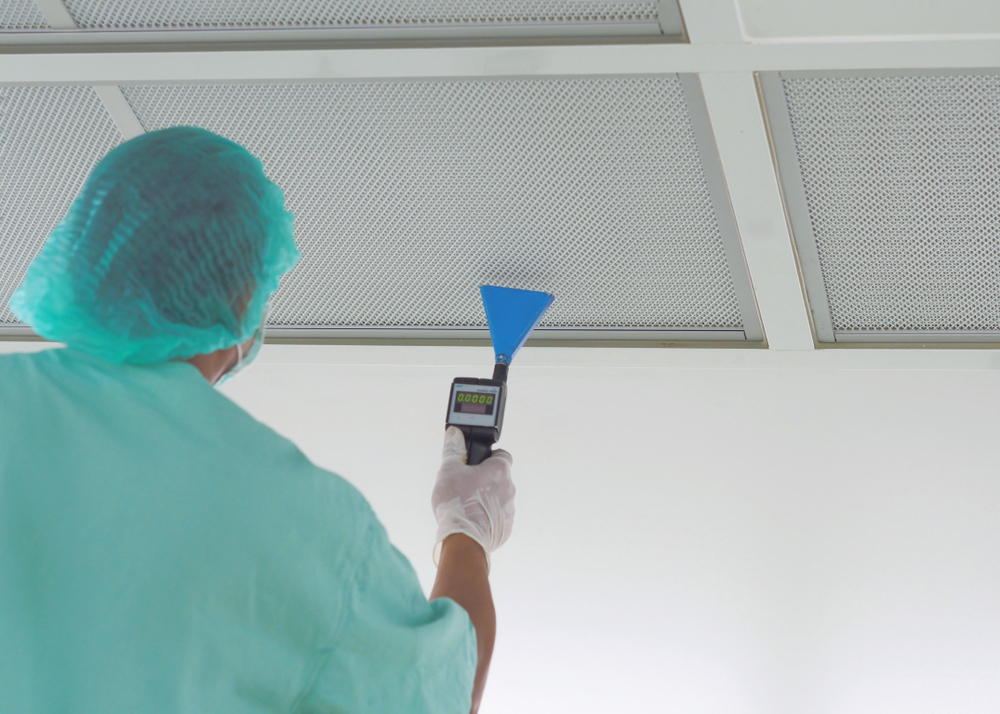
Other Tests
In addition, tests like non-viable particle counting and pressurization testing can provide further insight into the cleanroom’s functionality. Ultimately, the primary factors for assessment are the speed, balance and pressure of dual air patterns (which direct air through specific channels) and the amount of airborne particles present.
At SEPS, testing cleanroom features is one of the fundamental practices our technicians regularly perform. Decades of experience and practical knowledge enable us to verify with total confidence that a cleanroom is operating as per its requirements.
Cleanroom Certification
Like testing, the purpose of lab equipment certification is to confirm overall safety and efficiency. Additionally, they’re both a means of verifying that the cleanroom works according to its specific parameters and ISO classification. Usually, the first certification occurs once construction is complete. This confirms that the cleanroom meets each of the client’s specific requirements for their respective industry. Then, at regular annual or semi-annual intervals, an expert technician will repeat testing techniques to ensure stable performance and consistent quality.
Each certification should consider the location of the previous test. Specifically, the client must disclose the state. Also, it’s not uncommon to test and certify a cleanroom renovation or contamination issue. Technicians determine the specific tests once they evaluate several variables like standard requirements, auditing agency or a client’s specific needs.
Once each test is complete and the agency can verify all is functioning properly, they will certify the equipment with official documentation. SEPS technicians perform each cleanroom test
in accordance with current good manufacturing practices (cGMP). We follow strict (IEST) Institute of Environmental Sciences and Technology and (ISO) International Organization for Standardization guidelines.
Our Commitment at SEPS
At SEPS, our commitment to safety and efficiency governs absolutely everything we do. Our enduring respect for scientific industries motivates us to continuously deliver excellence for each of our clients. Of course, this applies to our testing and certification as well as our equipment maintenance, for cleanrooms and a variety of other scientific essentials.
